Energy in all its forms needs to be managed efficiently and cogeneration has moved to the forefront of optimized energy use and technology. This article is about understanding cogeneration plant efficiency calculation and how combined heat and power (CHP) systems can lead to more efficient facility operations.
Today’s power plants are making design changes that now include cogeneration, also known as CHP. When cogeneration is implemented efficiently, there is an opportunity to save between 15% and 40% of total energy consumption.
What is cogeneration and how does it improve efficiency?
At the most basic level, cogeneration engineering is a simple process. It makes use of the simultaneous production of both electricity and heat.
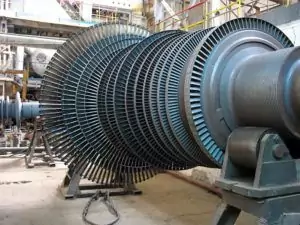
In a typical industrial power plant, electricity is created by using a steam-driven turbine or reciprocating engine. Steam can be produced by burning coal, natural gas, petroleum, or nuclear fission. While these plants generate electricity, they also generate large amounts of heat.
Cogeneration works by capturing that otherwise wasted heat and repurposing it to produce more electricity, heat utility fluids, or heat the air inside buildings. As a result, power plants that make use of cogeneration can operate with as much as 50-70 percent higher energy efficiency. This translates to both increased profit and sustainability.
Since cogeneration makes for more efficient use of available resources by recycling wasted heat, it reduces the reliance on fossil fuels.
Outside of power plants, cogeneration equipment is also used in sectors that rely on large amounts of both electricity and heat. These include:
- Pulp/paper
- Chemicals
- Refining
- Food processing
- Ethanol production
- Manufacturing
Typically, these facilities use natural gas as their primary fuel source, especially if natural gas pipelines can be found in close proximity to a given industrial plant.
How does cogeneration save energy?
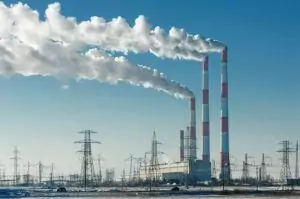
The effectiveness of a cogeneration package design depends on how well it delivers the created heat to the end-user. Most cogeneration plants will use hot water to create steam, which then transmits that heat. This means the geographical distance between the CHP package and the energy recipient is a vital component of maximizing cogeneration efficiency.
Cogeneration is best adopted as a decentralized process of energy supply. Building more smaller plants close to communities and consumers enhances CHP efficiency because there is less energy loss through resistance. As well, if excess energy is sent to the power grid, any residual waste is further reduced, which then transfers into savings for both the plants and the consumers.
Understanding cogeneration efficiency calculation
Cogeneration makes sense because it saves on the overall cost of fuel inputs. It does this by making use of a significant percentage of the energy from the designated fuel source.
Using one of two calculation methods, it is relatively simple to evaluate the total system efficiency and identify electric efficiency:
Total System Efficiency
This is the measure that is most used to make comparisons between the cogeneration process and the traditional, outdated, and conventional energy creation methods. This metric can be used to compare the overall efficiency levels of cogeneration, as opposed to conventional supplies alone.
Effective Electric Efficiency
This measure is for those plants that wish to compare the electricity generated by cogeneration versus conventional electricity production. This is usually related to the electricity produced using energy supplied by a grid.
Key Terms Used in Cogeneration Efficiency Calculation
To understand the process of calculating the efficiency of cogeneration processes, it is necessary to understand several key terms. These are:
CHP System
This refers to the entirety of the system being used to generate energy. It includes all the elements of the prime mover, including the combustion engine itself, as well as the microturbines and reciprocating engine models that are being used and the electricity generator. The core of the CHP system is the heat recovery unit that allows for cogeneration, transforming potentially wasted heat output into thermal energy that can be added to the overall output.
Total Fuel Energy Output
This is the total heating value of the fuel output of the facility. It is essentially a record of the total end-sum of the fuel that is being used by the CHP system. To calculate the total fuel energy output, it is necessary to multiply the total quantity of consumed fuel by the heating value of that fuel. Natural gas, coal, and diesel fuel will have different parameters of acceptability when it comes to total fuel energy output.
Net Useful Electric Output
This is the gross electric generation of your generator. It requires assessing any minuses in electric output through parasitic losses. The final figure for net useful electric output is simply the electric generated that can be used. When running a cogeneration efficiency calculation, it is essential to factor in those parasitic losses. This is usually the energy being used by the CHP system itself.
Net Useful Thermal Output
Cogeneration systems use the heat that is created by energy creation. The gross thermal output of the cogeneration system is the final figure after evaluating and calculating the thermal energy that is not being utilized.
Total System Efficiency
This is the sum of the net useful electric output and the net useful thermal output, which is then divided by the total energy input. When looking at total system efficiency, the target is to aim for between 60 and 80 percent.
The Future of Cogeneration
When it comes to the supply of combined heat and power, the idea of cogeneration is at the forefront in both commercial and industrial settings all around the world. Even leading educational institutions are making use of cogeneration, with MIT being one of the more publicized examples of a private facility adopting cogeneration to lower the operational cost of powering and heating their campus.
As in the case of MIT and many other institutions and businesses, making use of the excess heat generated when creating power just makes sense from both a financial point of view, as well as an environmental point of view.