Flaring & Methane
“I am very concerned by the rate of flaring in Texas,” Wayne Christian, Chairman of the Texas Railroad Commission, said after a June 2020 webcast meeting with environmental groups and shale industry representatives.
“We cannot continue to waste this much natural gas and allow the practice of flaring to tarnish the reputation of our state’s thriving energy sector to the general public and investors on Wall Street.”
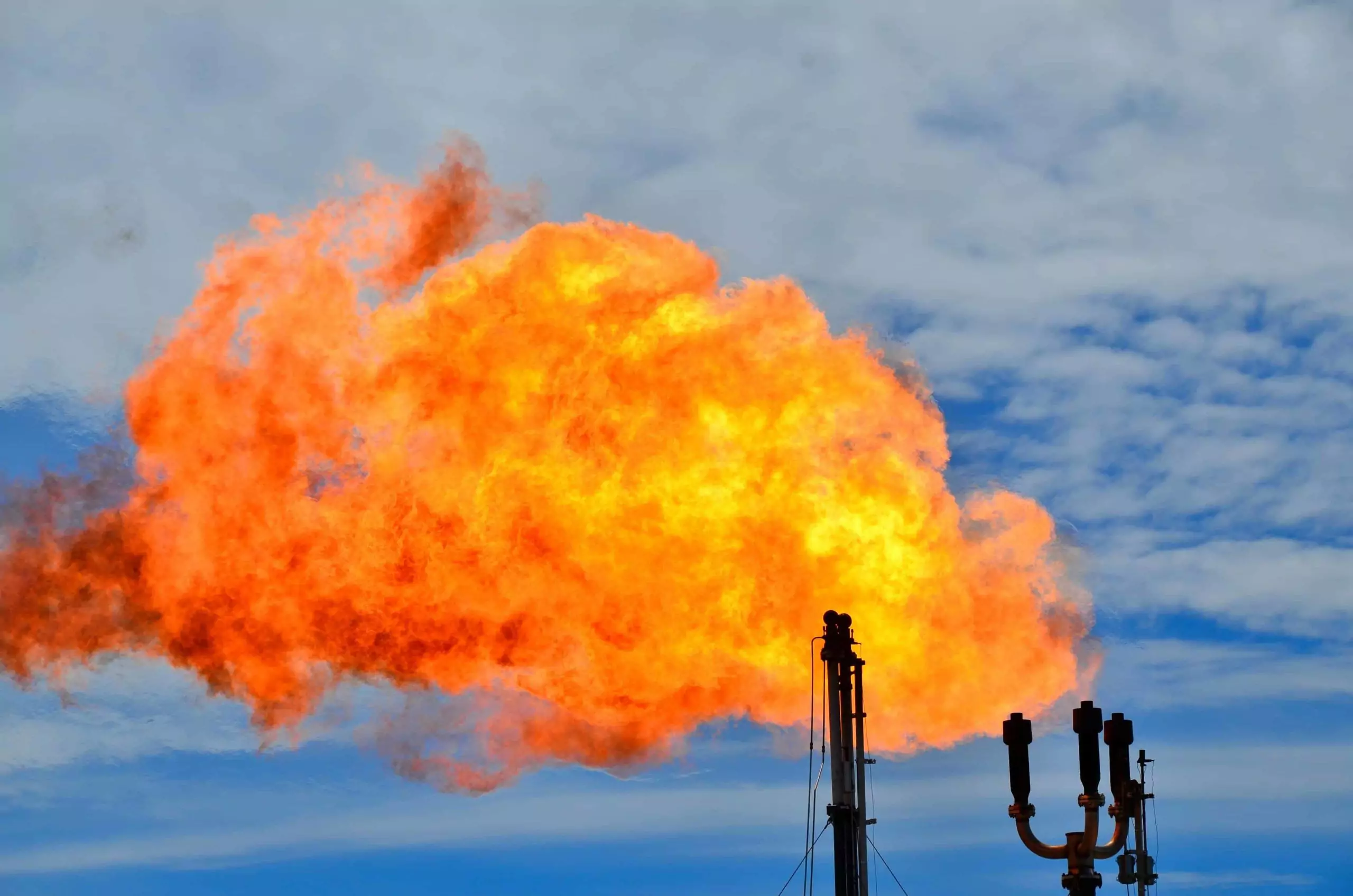
Environment Texas estimates that flaring in the US has increased four-fold since 2010. This is due to the increase in shale oil production, which also produces unwanted natural gas.
In Texas, many oil wells are in areas without gas pipelines, so shale producers apply to the Railroad Commission for permission to flare or vent the associated natural gas.
This graph from the Railroad Commission shows the recent correlation between oil production and flaring volumes in Texas.
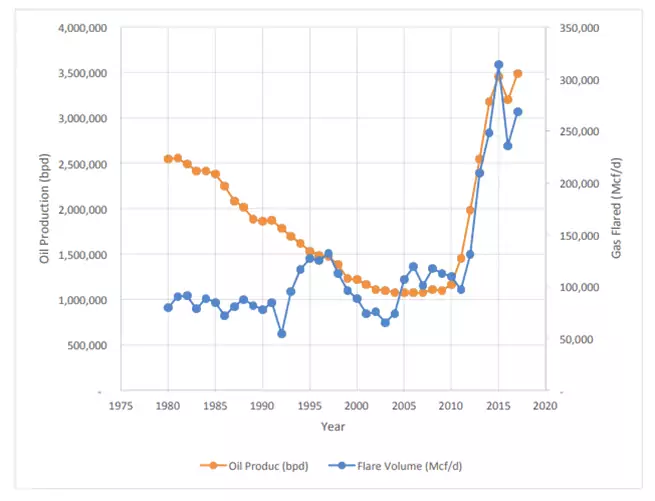
$750 Million in Wasted Gas
According to a report from the Institute for Energy Economics and Financial Analysis, “if the amount of gas flared in Texas in 2018 had been sold on the market, it would have brought $749.9 million to Texas oil producers.”
That’s a lot of wasted gas.
Economics aside, the environmental impact of flaring is also concerning. The flaring of natural gas releases carbon dioxide as it burns off methane. It has also been found that 10% of flares in the Permian Basin were malfunctioning, resulting in a direct release of methane into the atmosphere.
Methane (CH4) emissions are known to be a powerful climate pollutant that contributes to global warming. According to the US Environmental Protection Agency (EPA), natural gas and petroleum systems are the second largest source of methane emissions in the United States.
This is reflected in the October 17 GHGSat PULSE map of Texas, which colors the state mainly in orange and red, representing concentrations of methane over 1900 ‘parts per billion’ (ppb).
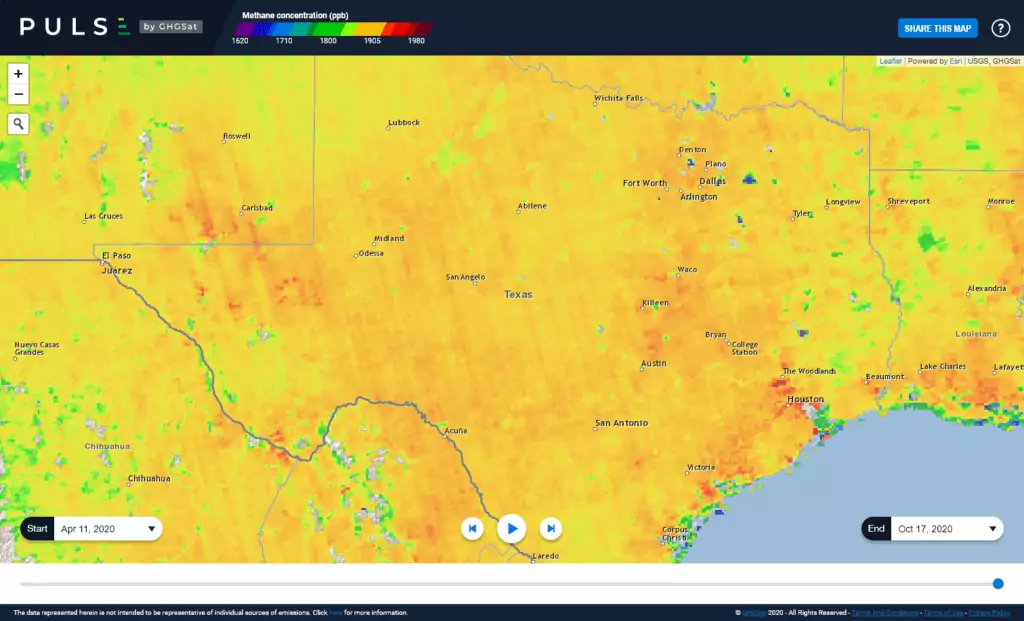
A Potential New Solution
Discussions around solutions to Texas’ flaring problem include:
- Shutting in oil wells with high flaring intensity
- Waiting for additional natural gas pipeline infrastructure
- Phasing out flaring completely
- Reducing flaring by adjusting the current permitting process
Cogeneration is one potential option that hasn’t gotten much attention but could simultaneously limit the economic and environmental impacts of flaring.
With one of Vista Projects’ industrial cogeneration units at the well site, oil producers could efficiently convert their natural gas to electricity that could then be sold back into the grid.
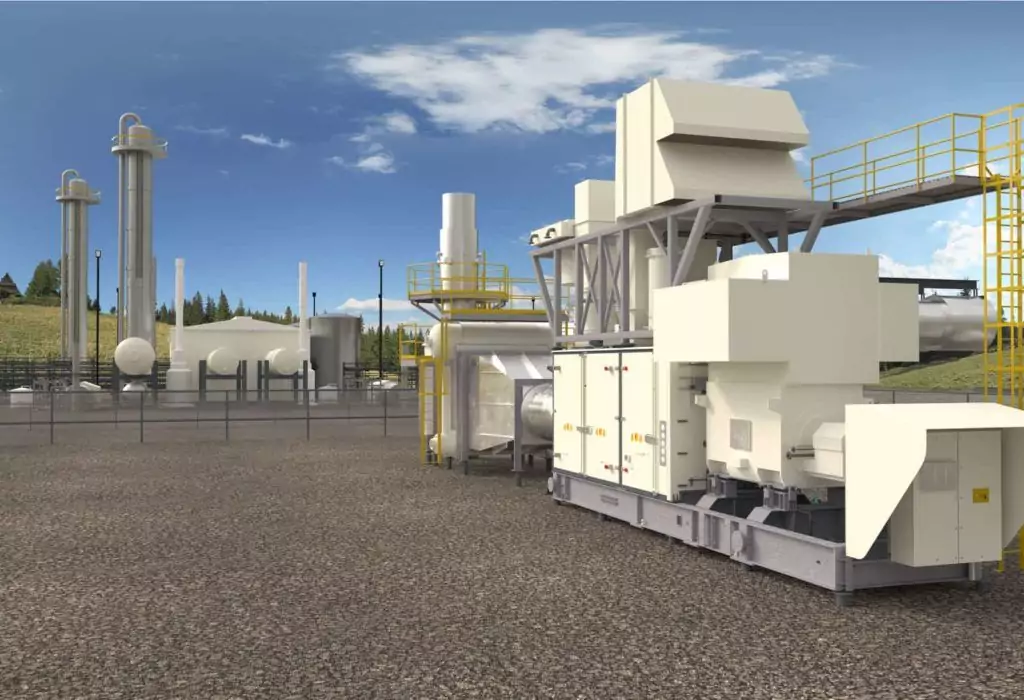
Allowing “grid edge” technologies to contract power back into the grid isn’t new. It helps system operators to balance supply and mitigate pricing spikes caused by excess capacity and shortages, which are often the result of unpredictable weather. During summer 2019, energy prices in Texas briefly spiked 25-fold, reaching north of $920 a megawatt-hour.
In June 2020, a bitcoin mining operation powered primarily by a windfarm near Midland became the first company to qualify as a “controllable load resource” with the Electric Reliability Council of Texas (ERCOT). The bitcoin miner is reporting 700% returns on its energy sales.
That sounds a lot better than flaring.
The Texas Commission on Environmental Quality (TCEQ) would seem to agree. TCEQ has a New Technology Implementation Grant (NTIG) Program that provides funding to “assist in the implementation of new technologies to reduce emissions of regulated pollutants from stationary sources.” In particular, the NTIG Program seeks technology in oil and gas to help “reduce flaring and other site emissions by capturing waste heat to generate electricity.”
Industrial Cogeneration
Industrial cogeneration systems could be a profitable and environmentally friendly solution to the flaring issue in Texas.
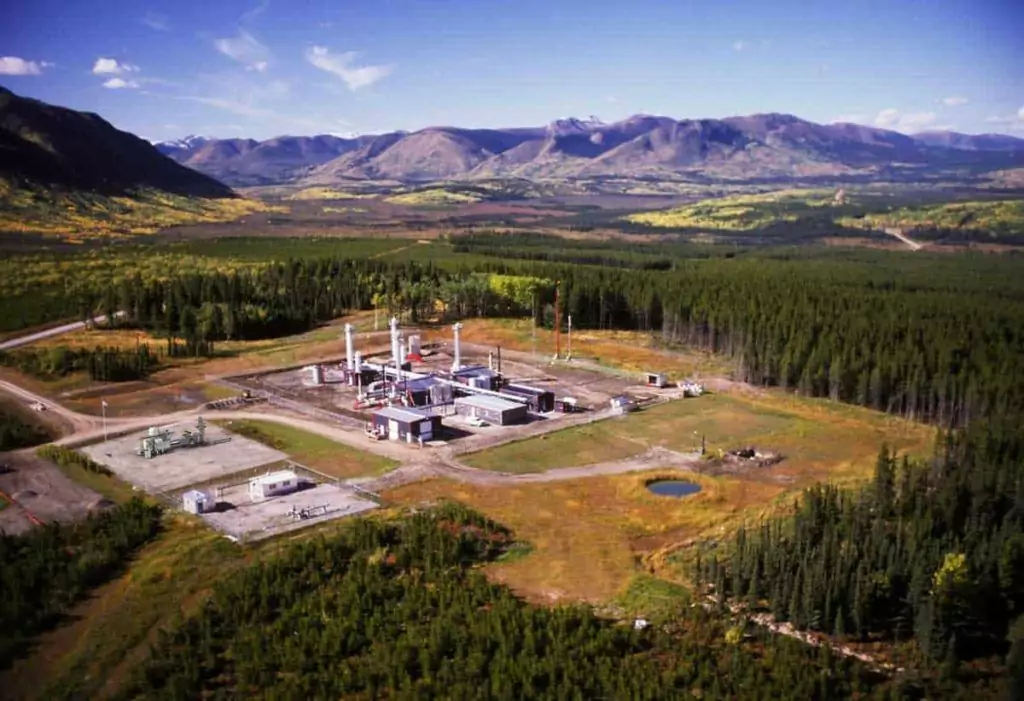
With a generating capacity of 5-25 MW and a condensed footprint of only 1,250 m2 (25m x 50m), Vista Projects’ industrial cogeneration units represent a viable carbon-reducing, grid-edge solution for the excess natural gas associated with shale oil wells.
Based on Vista’s leading industrial cogeneration engineering experience, the company believes the use of small-scale combined heat and power (CHP) systems at oil wells could reduce flaring activity in Texas by converting natural gas into electricity that could be sold back into the grid.
Combining simple cycle power generation from a gas turbine (GT) with a heat recovery steam generator (HRSG) could allow Texas oil producers to reduce methane emissions and increase profits.
The benefits of industrial cogeneration in the Texas shale oil sector include:
- Limited physical footprint (land disturbance)
- Lower CO2 and CH4 emissions when compared to flaring natural gas
- Increased profit by converting excess natural gas into electricity that can be sold back into the grid
This industrial cogeneration option should be of interest to operators of shale oil wells that flare associated natural gas in Texas or other jurisdictions.
Unit Specifications
Vista’s industrial cogeneration system was designed specifically for remote industrial applications with larger power needs and/or stable natural gas supplies.
System Overview
- Output capacity: 5 MW – 25 MW
- Condensed footprint: 1,250 m2 (25m x 50m)
- Operating pressure: 150 psig (1,034 kPag)
- Electrical generation: gas turbine generator (GTG)
- Steam production: heat recovery steam generator (HRSG)
- Dual heat delivery: exclusive GTG exhaust gas or combination of GTG exhaust with additional fuel gas
More About the Advantages of Industrial Cogeneration
Would your project or asset benefit from a stable supply of off-grid energy? Contact Vista Projects today to learn more about how their industrial cogeneration systems can provide 5 MW – 25 MW of high-efficiency combined heat and power.