Market Overview
Enhanced oil recovery (EOR) or tertiary recovery, is the process of extracting oil from an oil field or a reserve that would otherwise be inaccessible using conventional production technology. EOR techniques extract greater volumes from a reserve by altering the oil’s physical properties (i.e. viscosity/density).
There are three primary processes of tertiary or EOR extraction:
- Thermal recovery
- Gas injection
- Chemical/Solvent injection
Projected to reach $89.22 billion by 2025, the enhanced oil recovery market is rapidly growing and requires experienced facility engineering designs to improve recovery methods.
Experience Overview
Vista Projects has engineered facilities that are on the cutting edge of enhanced oil recovery (EOR) technology. Achievements working on a variety of EOR projects include:
- Reduced piping quality and cost through plot plan optimization
- Eliminated the need for water treatment unit using EDTA (Versene) as a softening option
- Reduced pumping HP requirements by introducing alkaline and surfactant chemicals upstream of the polymer injection pumps
- Reduced the necessary temperature for heated water heating, saving operational production expenses
- Implemented alternate caustic solutions (sodium hydroxide vs. soda ash)
We offer clients our expert knowledge of EOR techniques:
- Alkaline surfactant polymer (ASP)
- CO2
- Diluent recovery
- Miscible, polymer, and water flooding
- Polymer blending
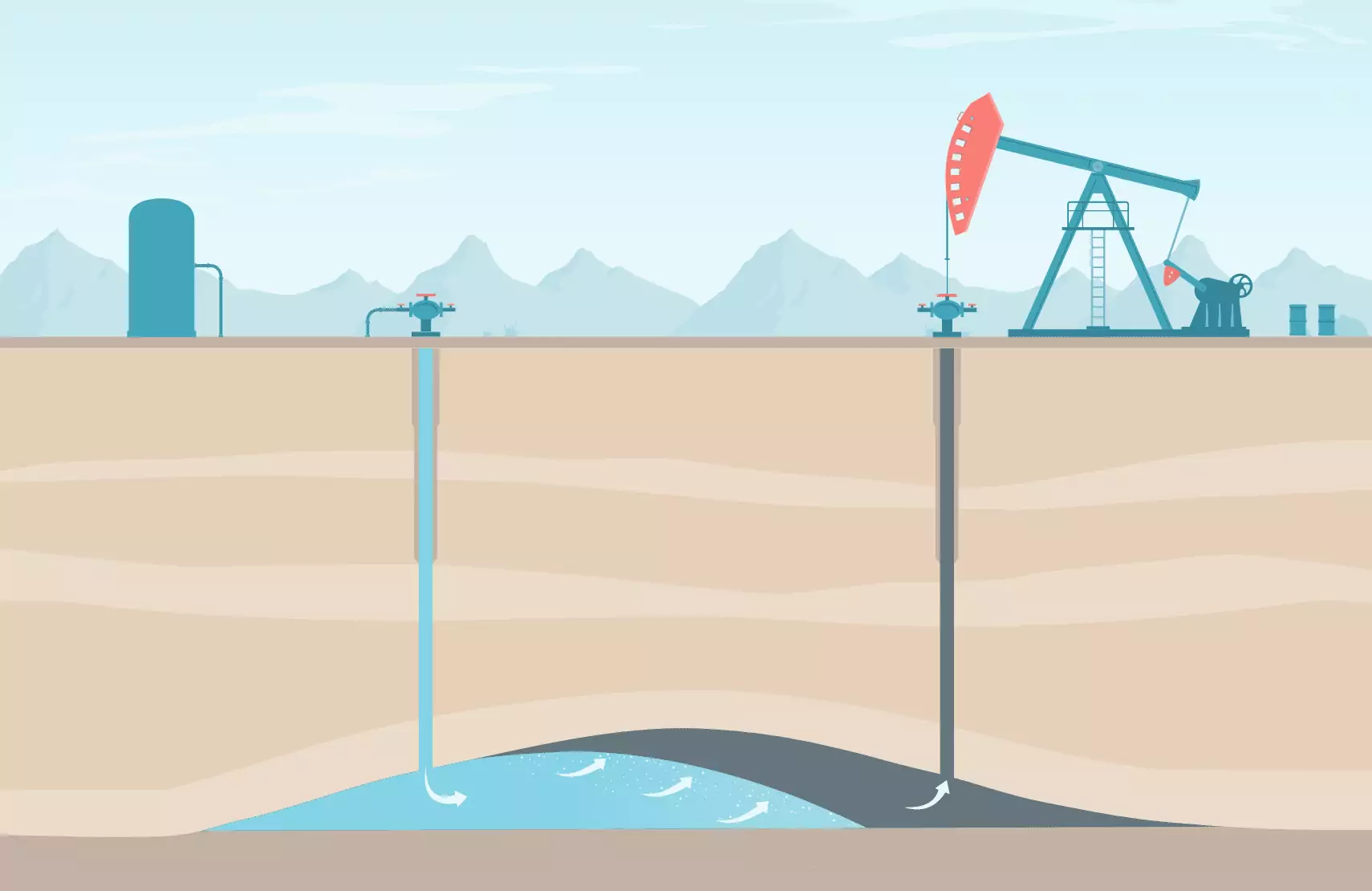
As an engineering firm, Vista Projects also has extensive experience with utilities, tankage, and well pad & pipeline development. Our project history includes long-term brownfield programs and multi-phase greenfield expansion projects.
Highlighted Projects
Alkaline Surfactant Polymer (ASP) Injection Flood
Vista worked with its client to design an alkaline surfactant polymer (ASP) injection pilot facility for use in the client’s Bakken oil production zone in southern Saskatchewan. The project’s design specifications called for an injection capacity of up to 800 m3/day of the polymer. Vista conducted the pre-FEED, FEED, and procurement for the project within specified timelines and budgets. The ASP package was comprised of:
- two SNF skids and an alkaline silo, used to mix, blend and inject surfactant, alkaline (soda ash), and polymer
- a source-water treatment system for hardness removal
- tanks for raw water, soft water, surfactant and wastewater
- source water pipeline from the source water well to the ASP facility
- four individual polymer injection pipelines from the ASP facility to four injection wells
Pipeline & Facilities for Miscible Flood
Polymer Flood Expansion
- polymer hydration skid
- water treatment facility
- various 2,000-barrel water tanks
- MCC expansion
- polymer injection skid
Related Brochures
Looking for more information? Download one of our related brochures to learn more about Vista Projects’ engineering consulting services.
Project Experience Overview
Modularization Optimization
Engineering Capabilities
Vista Projects has successfully engineered cutting-edge EOR facilities. Our focus on fit-for-purpose engineering designs and a data-centric approach to project execution are of great value in the EOR market, where cost efficiency is of great importance.
Alkaline Surfactant Polymer (ASP) Flooding
Alkaline Surfactant Polymer (ASP) flooding is an EOR method that involves injecting alkaline chemicals, surfactants, and polymers into the reservoir to decrease surface tension and enhance oil flow.
Diluent Recovery
A diluent is typically blended with bitumen extracted in an EOR facility before the bitumen is transported in a pipeline. Once the bitumen is delivered to its final destination (typically a refinery or upgrading facility), the diluent may be extracted from the bitumen and re-used for blending purposes.
Miscible Flooding
Miscible flooding involves injecting miscible gases into a reservoir to extract oil. Gases, like nitrogen and carbon oxides, as well as hydrocarbon gases, such as butane and propane, are typically used in the process. The process reduces the viscosity and density of the oil, thus making it easier for it to flow from the reservoir to the surface.
Polymer Blending and Flooding
Polymer Blending
The Polymer Blending EOR technique mixes dry polymer with water in a reaction tank to create a concentrated polymer solution that is then sent to a dilution tank for ageing, before being sent to the injection well.
Polymer Flooding
Polymer Flooding is an EOR technique that increases water viscosity to reduce the ratio of water to oil, using soluble polymers. The high viscosity polymer solution is more effective than pure water at sweeping oil from the reservoir to the producing well. The two polymers typically used for the process are:
- Xanthan
- Partially hydrolyzed polyacrylamide
Water Flooding
Water flooding is another EOR method which involves injecting water to expand the oil-production rate of reservoirs. Water injection increases reservoir pressure and helps move oil towards the production well.
What Our Clients Say
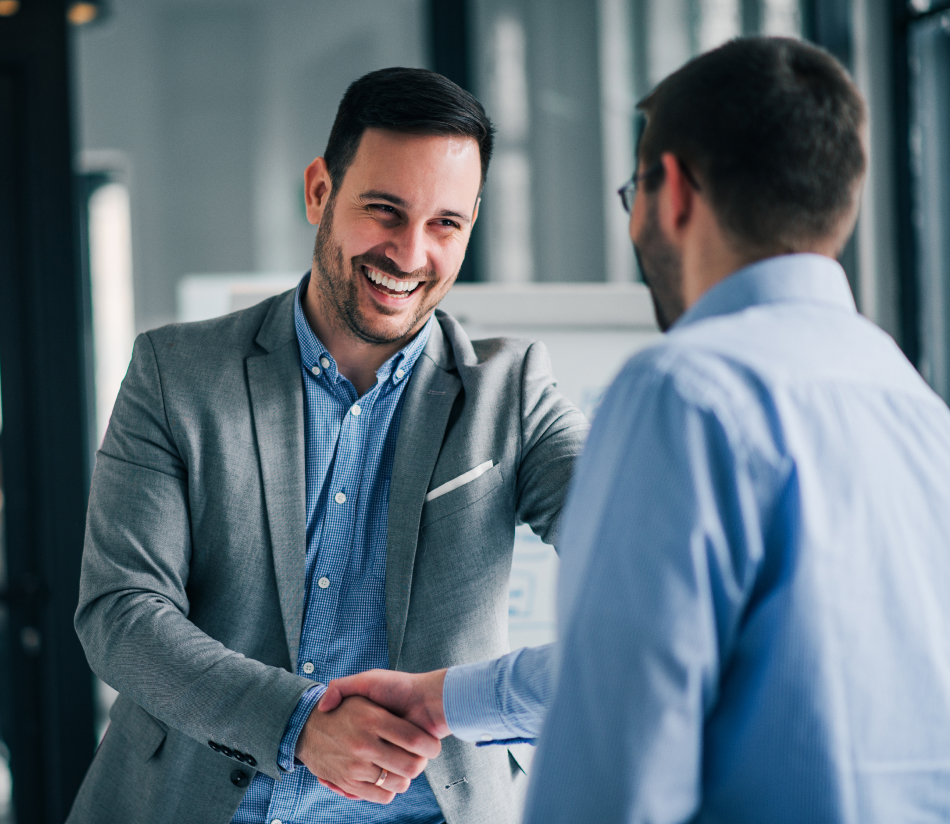
Improve your project success with the help of seasoned experts
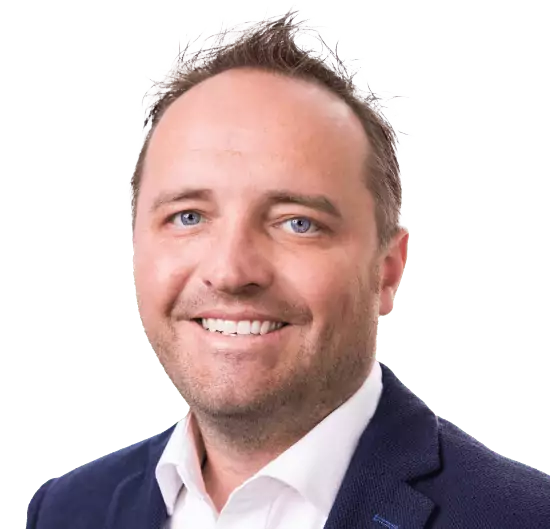
Tyler Elchuk
Business Development Director
All Clients Deserve
A Single Source of Truth
Our unique truth-based industrial engineering execution model facilitates:
- Transparency about projects and assets
- A collaborative problem-solving approach
- High-quality engineering designs
By structuring data in a single-source-of-truth (SSOT) environment, we simplify the digital transformation of your asset and help you make more informed decisions. Learn more about our system integration services.